Application Engineer Co-op: Applied Plastics
From July to December 2024, I completed my first co-op as an Application Engineer at Applied Plastics.
​
Applied Plastics is a leading manufacturer and supplier of coated components to the advanced catheter industry. They can maintain the tightest tolerances and apply a superior lubricious coating to mandrels and fine wire used in catheter manufacturing. Applied Plastics continues to find innovative coating solutions and processes for many different applications in the biomedical industry.
​
Although I am not able to go into complete detail about the projects I worked on at Applied Plastics, I am able to describe the different responsibilities and skills that I acquired under this role
Click on the image below to visit the company website!
​
​
​
Custom Catheter Components
At Applied Plastics, I developed 100+ 2D./3D models of custom catheter components. When a customer requested a quote for a unique component, I would create a Customer Reference Drawing on Adobe Suite that accounted for coating thickness based on the application of the component (mandrel, hypotube, pull-wire, etc.). Additionally, I would recommend certain critical dimensions and tolerances to customers to ensure grinding manufacturability. Next, I would design the 3D model in SolidWorks and create a 2D engineering drawing. I would also complete this process for changes to old parts by making a redline.

Skills Learned:
SolidWorks, Adobe, DFM, Customer Service, Redlines
QMS, Quoting, and Contract Review Meetings
After creating the engineering drawing, I submitted change orders with all of the appropriate documents through Applied Plastic's Quality Management System (QMS). I would also up-rev redlined prints through the QMS. Once the prints were approved, I would request quotes from a variety of vendors in order to maintain competitive prices. Often times, I would work with both the vendor and the customer to ensure tolerances and critical dimensions could be held and measured. I would do so in a timely manner to increase the speed of the quoting process at Applied Plastics.
​
At Applied Plastics, there is a daily special contract review meeting to provide updates on these quotes to the leadership team. The CEO, Director of Quality, and the Director of Internal Sales were all present. I ran 15+ of these meetings, in which I communicated updates on quote statuses, discussed manufacturability and coating capabilities for incoming customer requests, and answered any questions from members of the team.
.jpg)
Skills Learned:
QMS, Revision Control, Public Speaking
Mechanical Testing and Analysis
At Applied Plastics, I completed 150+ mechanical tests to obtain results used to improve new coating solutions. I conducted COF (coefficient of friction) tests using the ADMET machine (see image below), Tensile Tests using the Instron Tensile Test machine, RMS (surface roughness) tests using a Surface Profilometer, and utilized Optical Microscopy technology to analyze metals. I also had exposure to Scratch Test equipment (Bruker Machine) and designed fixtures to improve mechanical testing.
​​
Applied Plastics had received a customer substrate complaint. To respond to the complaint, I researched, designed, and executed an experiment using the equipment described above. Through Microsoft Excel, I analyzed the results in graphical and numeric form. I then wrote up a Technical Report and documented said report through the QMS.
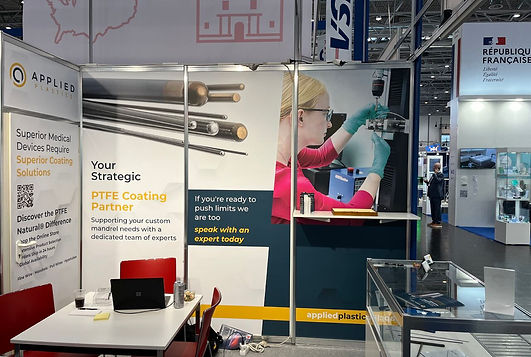
Skills Learned:
Technical Writing, Microsoft Excel, COF Testing, Instron Tensile Test, Optical Microscopy
Advanced Coating Fixture Design
There were multiple times at Applied Plastics where manufacturers could not adequately coat certain customized catheter components. In order to keep the business, I worked with the Custom Coating Supervisor to design customized fixtures.
Some fixtures were 3D printed. I collaborated with workers who specialized in coating to obtain all of the constraints, such as tolerances, critical dimensions, maximum temperature, and durability. Keeping these constraints in mind, I designed models on SolidWorks with the intent to be 3D printed. I then 3D printed these fixtures using material that was carefully selected so said fixtures could withstand certain forces and temperatures throughout the coating process.
Other fixtures were milled and welded by mechanics at Applied Plastics. I met with coaters, mechanics, and the Custom Coating Supervisor to collect all constraints to create a design that met expectations while also being easily machinable. Using the feedback from all parties, I developed SolidWorks drawings of prototypes for these complex fixtures with the intent for milling and welding. I led the design process and saw the fixtures go from a problem statement to a prototype, to testing, to designing and building the final model, and to finally documenting the fixtures.
​
Designing these fixtures has not been done before by previous co-ops. It became an integral part of R&D work at Applied Plastics. The Custom Coating Supervisor wanted the work to continue past my co-op term. In order to ensure efficiency for this transition process, I developed a document for the incoming co-op to provide context to my prior design projects.
.jpg)
Skills Learned:
DFM (3D Printing, Milling, Welding), Design Process, Leadership